Cad, Pdm and simulation make innovation fly at Italkrane, the leader in lifting equipment
by Piero Macrì ♦︎ The Milan-based company is a major player in lifting equipment. Customers include Saipem, Eni, Wood, Tecnimont, Daewoo, Hyundai, Samsung, Qatar Energy, and Cern. To innovate, the company relies on Cadac Group, which supports it in customising Autodesk and Ansys software. For example, Inventor and Vault. Integrations that break down information silos and simplify traceability. And on AI… we talk about it with Paolo Cavandoli, executive chairman and managing director of Italkrane
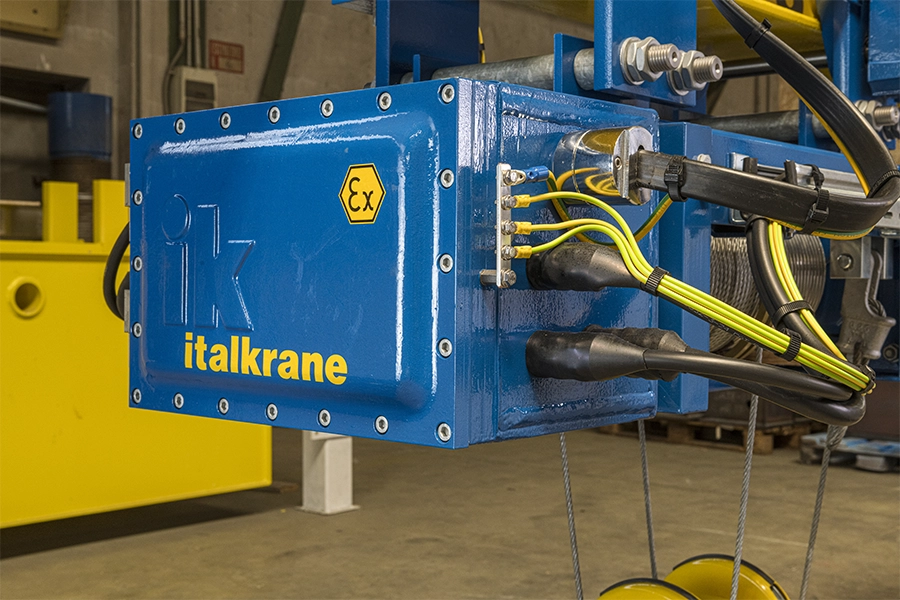
Italkrane was founded in Milan in 1962 by Enzo Banfi and Giovanni Penati, respectively CEO and chairman of the company until 2015 and still majority shareholders. The company, as mentioned above, offers complete lifting equipment, but also offers the supply of only the electromechanical components required to build cranes.
Engineering capacity, the result of a long-standing manufacturing tradition and often unique know-how, has always been the competitive factor of Italian SMEs. Expertise that still allows them to design and produce customised, high quality, state-of-the-art machinery that is exported all over the world. This is the case of Italkrane, a company specialising in customised design and production of lifting and transport equipment, with certified experience in the manufacture of explosion-proof machines capable of working in hazardous atmospheres, mainly for the oil & gas sector. Founded in the 1960s, with headquarters and factory in Bussero, in the eastern hinterland of Milan, the company has a worldwide installation base of more than 8,000 devices distributed in more than 100 countries and in particular in the Arabian Gulf. Thanks to continuous investments in digital technologies, Italkrane has been able to go through several eras under the banner of innovation, arriving at the present without ever compromising either its growth or its focus on quality, factors that allow it to position itself at a worldwide competitive level.
The digital backbone for product development are Autodesk’s Cad-Pdm technologies and Ansys simulation tools. Solutions that are developed in partnership with Cadac Group, Autodesk’s Platinum Partner, and Ansys’ channel partner E3D. “Quote, design and production. Data sharing is no longer based on Excel sheets, but converges on a single platform. All this allows us to be flexible and adapt quickly to market needs, develop new products quickly and maintain a high standard of construction,’ says Paolo Cavandoli, executive chairman and managing director of Italkrane. Customers include all major main contractors and plant builders worldwide, including Saipem, Eni, Wood, Tecnimont, Daewoo, Hyundai, Samsung, Qatar Energy.
“Cranes are machines capable of lifting and moving heavy loads, up to 150 tonnes in our production range, but the ones we produce in our factory are distinguished for being explosion-proof, which makes them suitable for operation in extreme, explosive environments where safety is a top priority. Italkrane’s strength is therefore its engineering and tailor-made production capacity for product innovation and special solutions. For a major waste water treatment plant in Abu Dhabi, Italkrane built a polar crane, for example. “It allows more versatile handling than standard models and can be used to lift loads in any direction,” explains Cavandoli. Also of great importance is the supply of machinery to CERN in Geneva for the construction of the Large Hadron Collider, the particle accelerator that has a circumference of around 27 km and runs in an underground tunnel 100 metres deep.
Innovation in product development and digitisation based on the integration of Cad, Pdm and simulation. And in the future a possible integration of artificial intelligence
On the one hand, the three-dimensional design of Autodesk Inventor, which has revolutionised the way the company develops products, making it possible to visualise and analyse the mechanics of cranes in detail; on the other hand, Pdm solutions such as Autodesk Vault, which reduce paperwork, improving operational efficiency in the management of project and production information. Finally, the Ansys finite element structural simulation. “Through simulation, it is possible to accurately predict the behaviour of the structure when subjected to loads, temperatures and other stresses, avoiding costly experimental tests, it allows areas subjected to higher stresses to be identified, and it allows design changes to be made to improve the strength and durability of lifting equipment,” says Cavandoli. The relationship with Cadac Group proves to be crucial for developing software customisations. Thanks to the collaboration with the engineering team, for example, a customisation of the Cad Inventor environment was created that allows the precise calculation of painting costs for all crane parts. Even generative artificial intelligence, which is evolving today, is seen as a possible tool to automate the most repetitive tasks of design and document management. “From what we are finding out, the potential seems to be significant. Italkrane has always been attentive to any technology capable of offering new possibilities. On the other hand, careful planning is needed; we will invest in AI following evaluations and studies that make it clear what the actual return on investment will be,’ says Cavandoli.
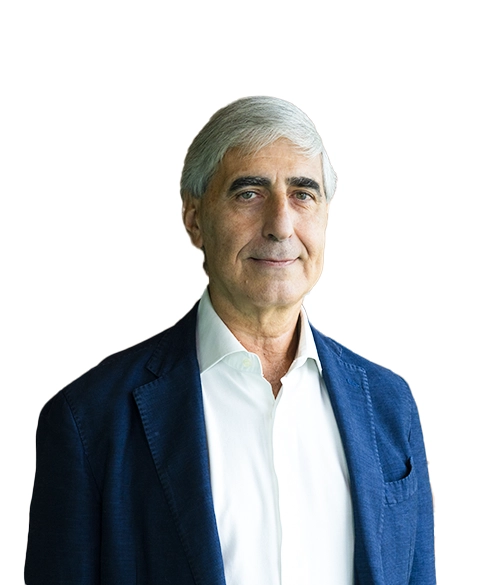
Paolo Cavandoli
Executive chairman and maraging director of Italkrane.>
The benefits of Inventor-Vault integration: a data flow that breaks down company silos and creates greater transparency and traceability of job data
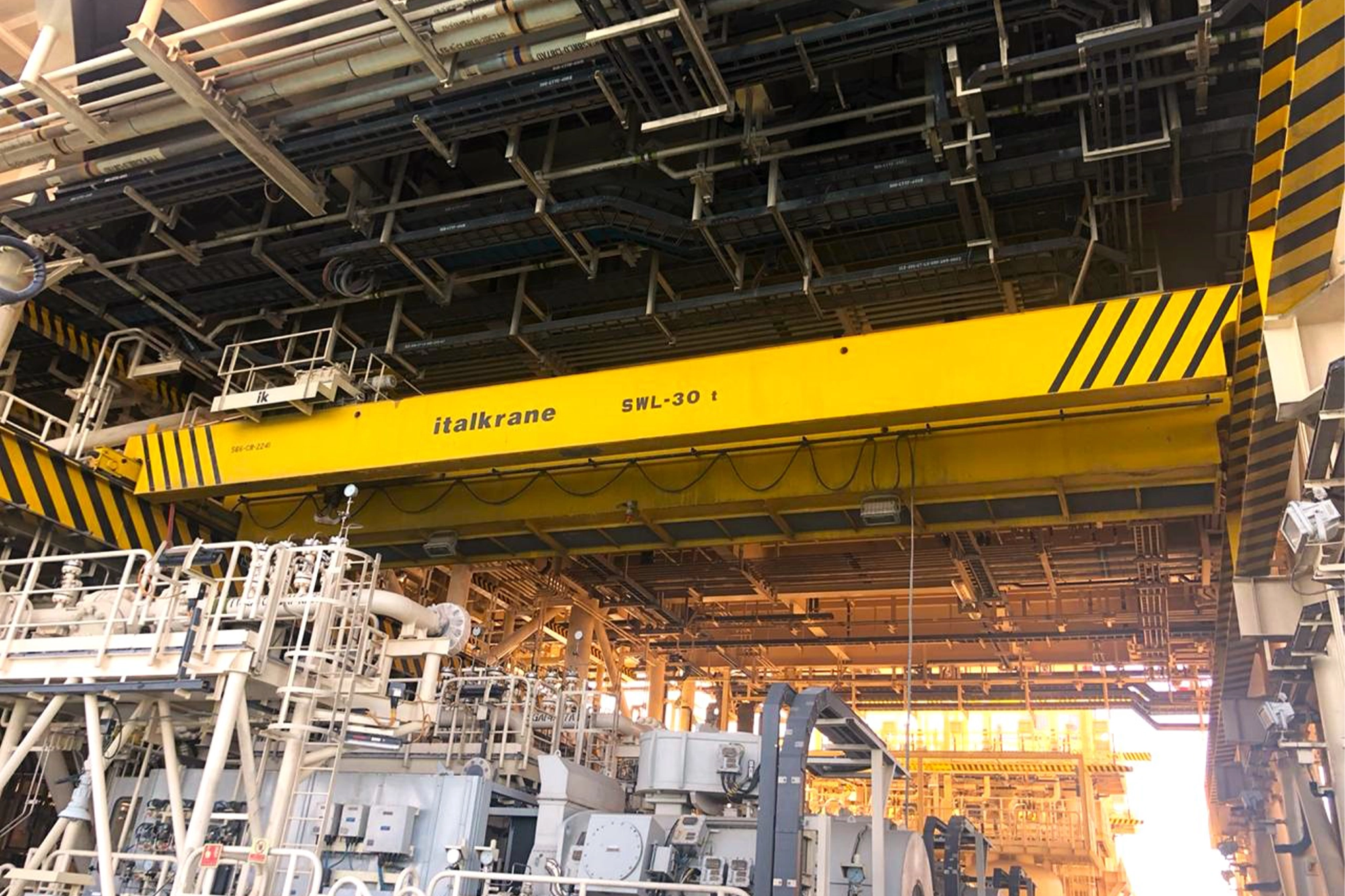
Cranes are machines capable of lifting and moving heavy loads, up to 150 tonnes in our production range. Italkrane cranes are also suitable for operation in extreme, explosive environments.
With Vault, all Cad files, related documents and project information are centralised in one repository, facilitating search and sharing. Autodesk’s Pdm software automatically tracks changes made to files, making it easy to retrieve previous versions and keep track of changes made over time. By eliminating the need to create multiple copies of a file, the proliferation of obsolete versions is avoided and data consistency is ensured. Access levels and authorisations can be defined for each user, ensuring that only authorised users can view or modify data. Project review, approval and release processes can be automated, reducing lead times and minimising errors. In this regard, Cavandoli states: “Vault provides tools for communication and collaboration between team members, simplifying information exchange and problem solving. It allows you to create a library of standard components, facilitating reuse and reducing design time.
The value of Italkrane? Design and production autonomy to realise highly innovative systems. The special feature of explosion-proof cranes with micrometer-precision movement speed
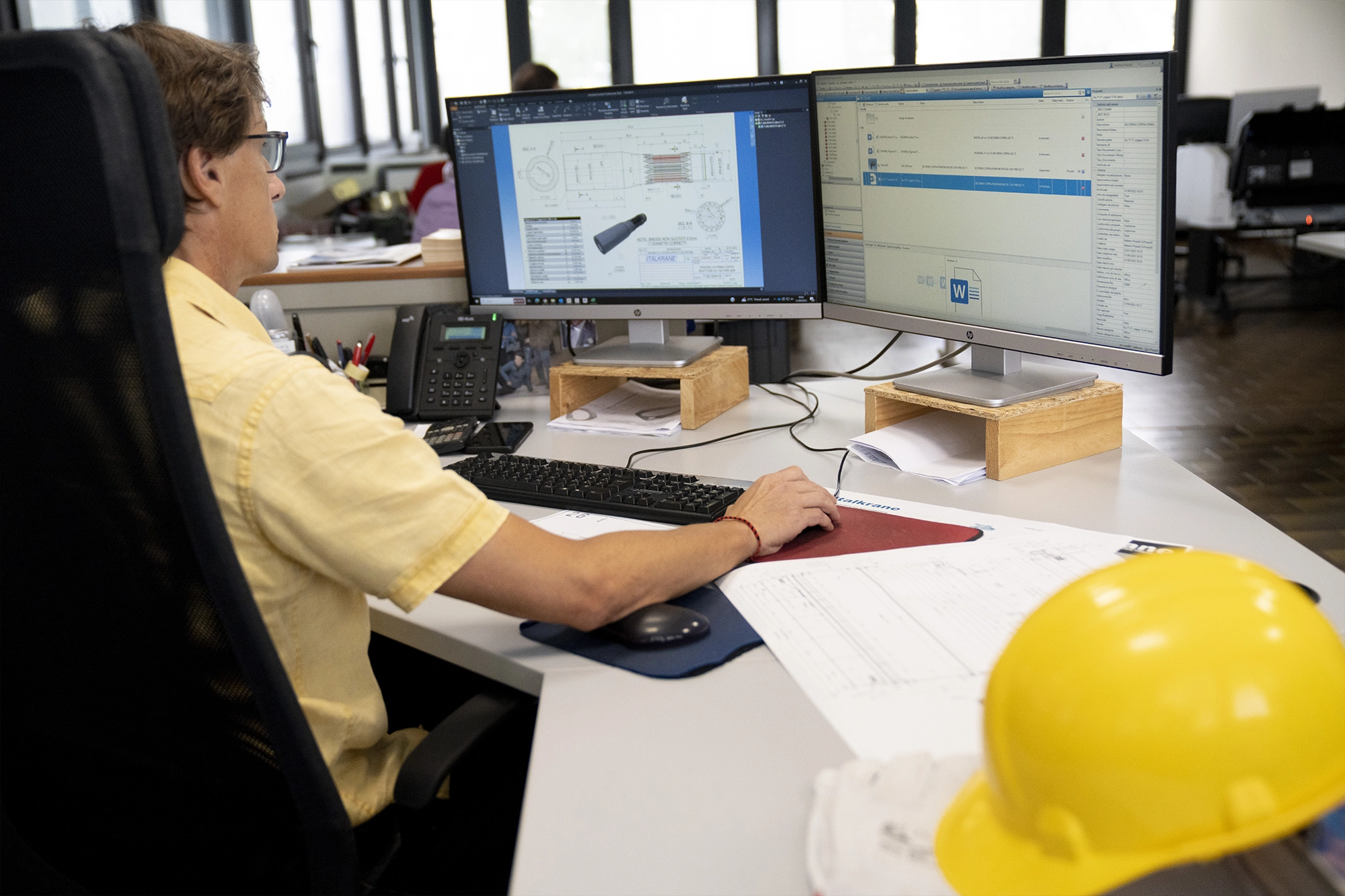
With Vault, all Cad files, related documents and project information are centralised in one repository, facilitating search and sharing. Autodesk's Pdm software automatically tracks changes made to files, making it easy to retrieve previous versions and keep track of changes made over time.
“We produce almost all components in-house, unlike many competitors who rely on external suppliers,” says Cavandoli. He continues: “Our approach allows us to maintain a high degree of control over quality and design, which is tailored to specific customer requirements. This, as already mentioned, includes the ability to design machines to operate in extreme environments, such as those with low temperatures or in the presence of potentially explosive substances. For explosionproof systems (Zone 1-21 IIB), we produce certified steel enclosures across our entire product range, which will soon be extended to include IIC type gases.
The Italkrane factory houses three large multiple machining centres, as well as welding and painting departments. This factory approach makes it possible to build machines with unique features, such as the option of micrometric lifting speeds thanks to the use of two separate motors combined with a differential. Each movement (lifting, translation, rotation) is controlled by a dedicated motor and this allows for greater precision and flexibility in manoeuvres, enabling simultaneous or independent movements to be performed as required. In this regard, Cavandoli says: “In recent years, projects have increased in value and complexity. This led to increased pressure on production and assembly, requiring continuous adaptation to new requirements. Today, many plant engineering companies are based, for example, in Italy, but with engineering in India and construction sites in Abu Dhabi, so coordination is far from simple. This can lead to different kinds of errors and longer design times due to frequent changes. Today’s market challenges mean that Italkrane needs to be as flexible as possible and to continuously improve processes and products, with the aim of remaining competitive in the market without penalising quality and safety in any way’,
Italkrane, over sixty years of experience in materials handling and production logistics
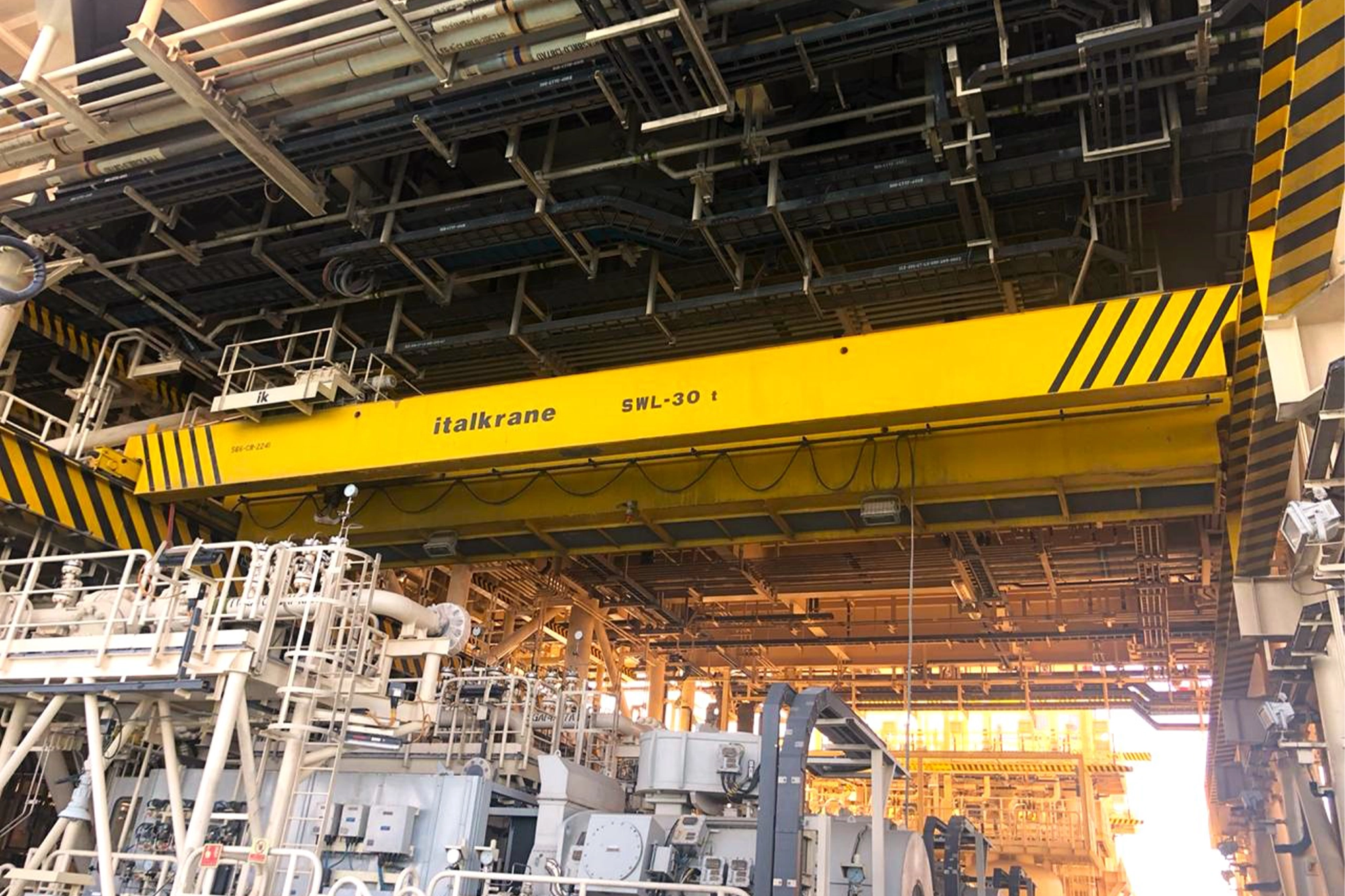
Overhead crane installed at the building of an Italkrane customer.
Italkrane was founded in Milan in 1962 by Enzo Banfi and Giovanni Penati, respectively CEO and chairman of the company until 2015 and still majority shareholders. The company, as mentioned above, offers complete lifting equipment, but also offers the supply of only the electromechanical components required to build cranes, with the exception of the relevant structures. On request, engineers and technicians not only provide construction drawings for the machinery, but also develop customised, non-standard solutions tailored to specific customer requirements. This ensures a high standard of quality and compliance with the latest national and international safety directives and laws. Once the design phase is complete and the necessary approvals have been obtained, Italkrane starts the production process using advanced technologies and high quality materials. Since these devices must work in highly critical industrial environments, including in contact with harmful substances and dust, all structural components feature anti-corrosive properties. Every component, from motors to wiring, is designed and certified to operate in explosive atmospheres with control systems that prevent the formation of sparks or the build-up of static charges.
Cadac Group, the one-stop shop for procurement of make & design solutions and expertise
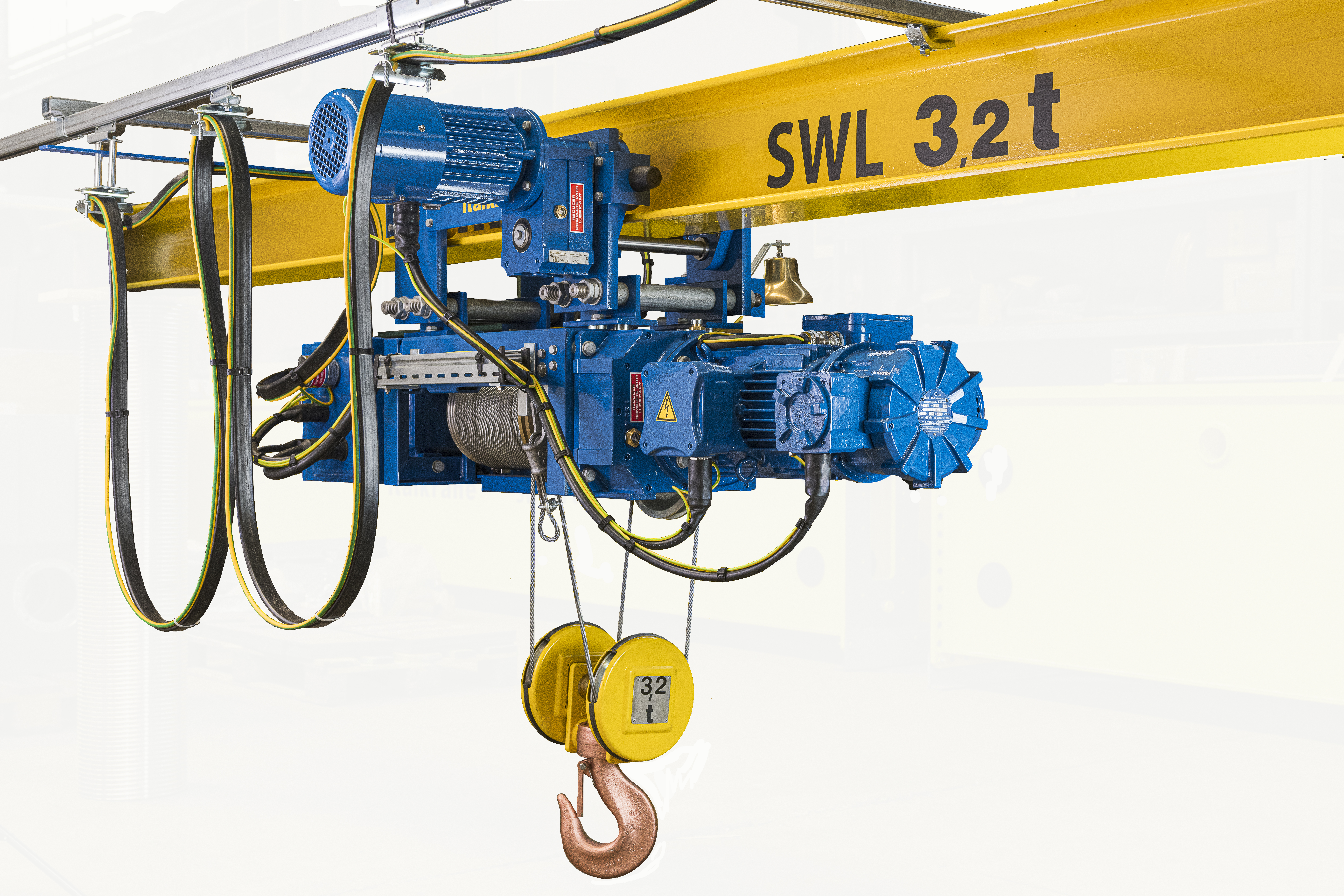
iItalkrane's customers include all the world's major main contractors and plant builders, including Saipem, Eni, Wood, Tecnimont, Daewoo, Hyundai, Samsung and Qatar Energy.
Cadac Group offers a comprehensive portfolio of solutions to support companies in the digital product development journey. Autodesk’s Platinum Partner, one of the most important in Europe, complements Autodesk’s software solutions with Ansys simulation technology, offered through its subsidiary E3D. Cad, Cam, Pdm, Plm, Bim, Simulation, the services offered across the entire application spectrum for digital transformation make Cadac the one-stop shop for procurement of make & design solutions and expertise. Headquartered in Milan (Paderno Dugnano) and branches in Crema, Bologna, Turin, Rome, Bari, Naples and Madrid, an extensive presence that ensures customer proximity, which is considered indispensable to market with a service offer. “Programmers, engineers. In Autodesk and Ansys, we have the skills and experience to support customer requirements independently,’ says Marco Luzzini ceo of Cadac Group’s Southern Europe countries. He concludes: “Data and Plm management, communication with the Erp environment and simulation for the development of digital prototypes. Opportunities are played out within this context and it is in this direction that we aim to extend our activities. It is important for us to guarantee the customer a return on investment of the different solutions. And we do this through a consultancy service, identifying purchasing methods and product types according to the objectives to be achieved’,